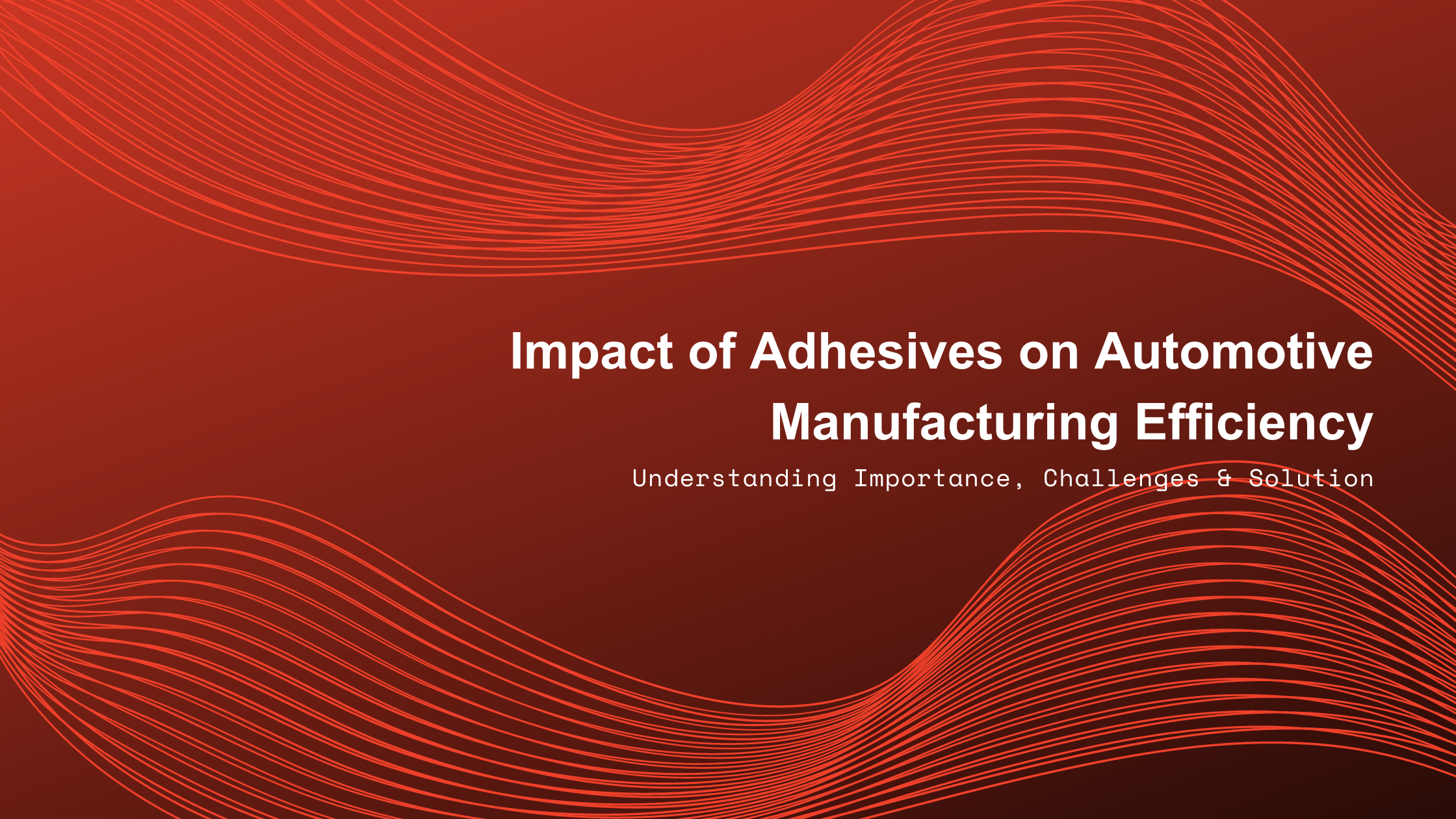
The Impact of Adhesives in Automotive Manufacturing Efficiency
In the intricate realm of automotive manufacturing, efficiency stands as a cornerstone of success. As technology propels the industry forward, the role of adhesives in enhancing efficiency emerges as a pivotal factor. This article delves into the profound impact adhesives wield in automotive manufacturing, from their historical roots to futuristic innovations. Adhesives in automotive play a crucial role in streamlining assembly processes, improving structural integrity, and driving innovation.
Automotive manufacturing is witnessing a paradigm shift propelled by technological advancements and consumer demands. Traditional methods are making way for innovative approaches aimed at streamlining processes and optimizing performance. In this dynamic landscape, adhesives emerge as silent heroes, revolutionizing assembly techniques and redefining industry standards.
Importance of Efficiency in Automotive Production
Efficiency is not merely a buzzword in automotive production; it’s a fundamental necessity. With consumer expectations soaring and competition intensifying, manufacturers are under relentless pressure to maximize productivity without compromising quality. Adhesives offer a pathway to achieve this delicate balance by enhancing assembly speed, reducing waste, and elevating overall operational efficiency.
Understanding Adhesives in Automotive Manufacturing
What Are Adhesives and How Are They Used in Automobiles?
Adhesives represent a diverse class of materials designed to bond surfaces together. In automotive manufacturing, they serve as the invisible glue holding various components in place, ranging from body panels to intricate electrical modules. Unlike traditional mechanical fastening methods like welding or riveting, adhesives distribute stress uniformly, resulting in enhanced structural integrity and durability.
The Evolution of Adhesive Technologies in the Automotive Industry
The evolution of adhesive technologies mirrors the progressive trajectory of automotive manufacturing. From rudimentary formulations to sophisticated composites engineered for specific applications, adhesives have undergone a remarkable transformation. Manufacturers now have access to a plethora of adhesive options tailored to meet the stringent demands of modern automotive assembly lines.
Challenges and Solutions
Compatibility and Durability
One of the primary challenges in adhesive application lies in ensuring compatibility with diverse substrates. Mismatched materials can lead to adhesive failure, compromising the structural integrity of assembled components. Innovative formulations and surface treatments mitigate this risk, enabling adhesives to bond seamlessly with a wide array of materials, including metals, plastics, and composites.
You may like also: How Adhesives and Sealants Improve Electric Vehicle Durability and Reliability?.
Temperature and Environmental Considerations
Automotive environments are rife with temperature fluctuations, moisture exposure, and chemical contaminants, posing significant challenges for adhesive performance. Advanced formulations engineered to withstand extreme conditions ensure reliable bonding, even in the harshest automotive environments. From scorching deserts to icy tundra’s, adhesives stand resilient, upholding the integrity of assembled structures.
Quality Control and Standardization
Maintaining consistency in adhesive application is paramount to achieving uniformity and reliability across production lines. Rigorous quality control measures, coupled with standardized application protocols, safeguard against variations in adhesive performance. By adhering to strict quality standards, manufacturers uphold the reputation of their brands while instilling confidence in consumers.
Advantages of Using Adhesives in Automotive Manufacturing
The adoption of adhesives in automotive manufacturing confers a multitude of benefits, transcending traditional assembly methods.
Enhanced structural integrity and durability
Adhesives distribute stress uniformly, mitigating the risk of fatigue failure and corrosion, thus extending the lifespan of assembled components.
Weight reduction and improved fuel efficiency
By eliminating the need for bulky mechanical fasteners, adhesives contribute to weight reduction, thereby enhancing fuel efficiency and reducing carbon emissions.
Noise, Vibration, and Harshness (NVH) reduction
Adhesives with viscoelastic properties dampen vibrations and absorb noise, resulting in a quieter, more comfortable driving experience. By minimizing NVH, adhesives enhance vehicle quality and customer satisfaction, setting new standards for automotive refinement.
Design flexibility and aesthetic improvements
The use of adhesives enables designers to explore innovative structural configurations and achieve seamless aesthetic integration, elevating the visual appeal of automotive interiors and exteriors.
Types of Adhesives Transforming the Automotive Industry
Adhesive technologies continue to evolve, offering a diverse array of formulations tailored to meet the unique demands of automotive applications.
Structural Adhesives
The structural adhesives that hold the automobile landscape together are polyurethanes, epoxy resins, and methyl methacrylates. Epoxy resins are used because they can form strong connections between metals, composites, and polymers. They are known for their strength and endurance. Methyl methacrylates are notable for their quick curing qualities, which guarantee quick assembly, while polyurethane adhesives provide flexibility, making them perfect for applications requiring resistance to impact.
Cyanoacrylate Adhesives
Known for their rapid curing and strong bond strength, cyanoacrylate adhesives find applications in bonding plastics, rubber, and metals in automotive assembly.
Rubber-Based Adhesives
The automotive sector relies heavily on rubber-based adhesives because of their special qualities and adaptability. Because of their famed flexibility, neoprene adhesives are the preferred choice for joining rubber to a variety of substrates. In the meanwhile, applications where exposure to oils and fuels is a problem find a home for nitrile rubber adhesives, which are highly valued for their oil resistance.
Pressure-Sensitive Adhesives
Characterized by their tackiness and conformability, pressure-sensitive adhesives adhere to surfaces upon application of slight pressure, facilitating quick and easy assembly of automotive components.
Thermoplastic Adhesives
Engineered to soften upon heating and solidify upon cooling, thermoplastic adhesives provide reversible bonding solutions suitable for rework and repair applications.
Anaerobic Adhesives
Activated in the absence of oxygen, anaerobic adhesives form strong bonds between metal surfaces, offering excellent resistance to vibration and corrosion.
Silicone Adhesives and Sealants
Renowned for their weather resistance and thermal stability, silicone adhesives and sealants seal gaps and joints, preventing moisture ingress and enhancing long-term durability.
Applications of Adhesives in Different Automotive Components
Adhesives permeate various facets of automotive assembly, serving as the adhesive backbone of critical components.
Body-in-white assembly
Structural adhesives facilitate the seamless integration of body panels, enhancing rigidity and crash resistance while minimizing weight.
Structural bonding of chassis components
High-strength adhesives reinforce chassis assemblies, optimizing vehicle dynamics and ensuring superior handling characteristics.
Interior trim and upholstery bonding
Adhesives provide a reliable means of bonding interior trim components, enhancing aesthetics and imparting a luxurious finish to automotive interiors.
Windshield and window installation
Silicone adhesives seal windshields and windows, providing structural support and safeguarding against water ingress and air leaks.
Electrical component attachment
Conductive adhesives secure electrical components, ensuring reliable connectivity and minimizing electromagnetic interference.
Challenges and Solutions in Adhesive Application
Adhesive application poses unique challenges that necessitate innovative solutions to ensure optimal performance and reliability.
Surface preparation and cleanliness
Effective adhesive bonding hinges upon meticulous surface preparation, encompassing cleaning, degreasing, and surface activation to promote adhesion.
Compatibility with different materials
Navigating the diverse landscape of automotive materials requires adhesives capable of bonding dissimilar substrates while maintaining long-term durability.
Temperature and environmental considerations
Adhesive formulations engineered to withstand extreme temperatures and environmental conditions ensure reliable performance throughout the vehicle’s lifecycle.
Quality control and inspection processes
Robust quality control measures, including adhesive testing and inspection protocols, safeguard against defects and ensure adherence to stringent quality standards.
Future Trends and Innovations in Automotive Adhesive Technology
The future of automotive adhesive technology is poised for groundbreaking advancements, driven by a relentless pursuit of innovation and sustainability.
Advancements in bio-based and sustainable adhesives
The advent of bio-based adhesives derived from renewable sources promises eco-friendly alternatives with reduced environmental impact.
Integration of smart adhesives with sensor technology
Smart adhesives embedded with sensor technology offer real-time monitoring capabilities, enabling proactive maintenance and performance optimization.
3D printing of adhesive structures for customized applications
The emergence of 3D printing technology enables the fabrication of intricate adhesive structures tailored to meet the unique requirements of automotive applications.
Conclusion
The impact of adhesives in automotive manufacturing efficiency is undeniable, shaping the future of automotive production. From enhancing structural integrity and durability to enabling lightweight designs and aesthetic enhancements, adhesives serve as catalysts for innovation and progress. As the automotive industry continues to evolve, adhesives will remain indispensable, driving efficiency, sustainability, and performance to unprecedented heights.
Post a comment