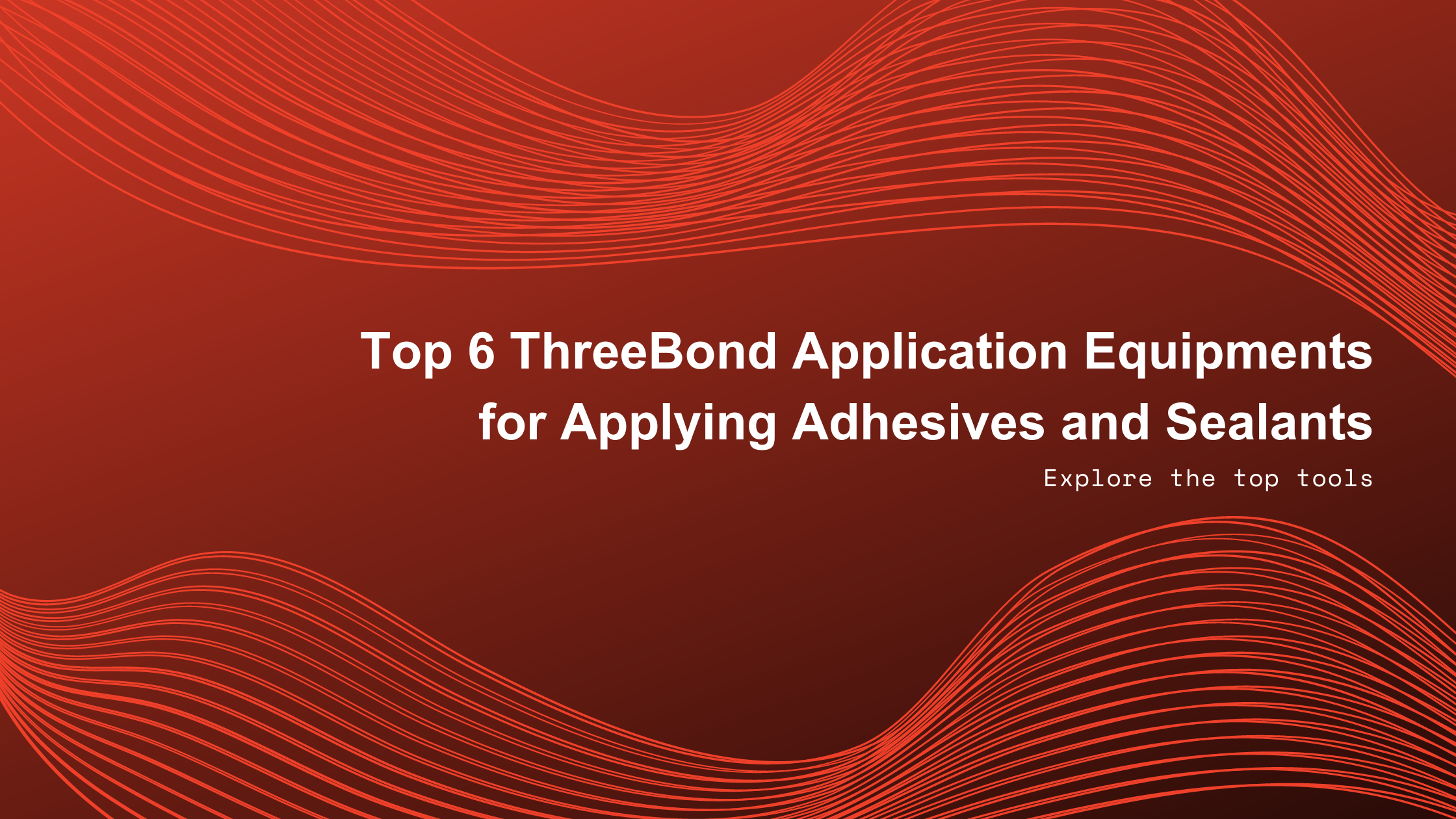
Top 6 ThreeBond Adhesive Application Equipments for Applying Adhesives and Sealants
Discover precision and efficiency with ThreeBond’s state-of-the-art adhesive application equipments. Here are the top tools that revolutionize adhesive and sealant application, ensuring quality and savings.
1. ThreeBond Sealant and Adhesive Application Equipments System
ThreeBond’s adhesive and sealant application system is engineered to provide precise, efficient, and high-quality application of sealants and adhesives. This advanced system is composed of a combination of a robot, LW booster, and pump, which together enable fixed-quantity dispensing for both low and high-viscosity materials. This ensures a consistent application speed and volume, which is critical for maintaining quality and reducing waste. With its state-of-the-art design, ThreeBond’s system stands out among adhesive application equipments for its ability to integrate seamlessly into existing production lines, providing superior performance and significant material savings.
Features:
- Fixed-Quantity Dispensing: Ensures consistent and precise application of a set amount of sealant or adhesive with every cycle, regardless of material viscosity.
- Integration with Existing Equipment: Designed for seamless integration with your current dispensing setups, minimizing disruption to existing workflows.
- Record-Keeping with LW Booster (Optional): Tracks the exact amount of sealant dispensed for each engine part, enabling proactive monitoring and quality control (additional purchase required).
- Compact Design and Safety: Features a space-saving design to maximize floor space efficiency and includes safety hand switches for operator protection.
- Material-Saving Tank: Reduces waste by capturing excess sealant or adhesive, potentially recovering pump costs within 3-4 years through material savings.
Benefits
- High Application Quality: Delivers consistent, superior results with every dispense, leading to a higher overall quality for your finished product.
- Operational Efficiency: Enhances precision and consistency in dispensing, improving productivity and reducing rework.
- Ease of Use: Simple integration and operation minimize downtime and training requirements for your workforce.
- Cost-Effective: Offers long-term savings from reduced material waste and potential pump cost recovery.
- Seamless Upgrades: Minimizes disruption to existing production lines, allowing for a smooth upgrade process.
- Enhanced Quality Control (Optional): Provides valuable data on dispensed sealant quantities for each engine part with the LW Booster, enabling proactive identification of potential issues (additional purchase required).
2. Advanced Power Booster Model PBIII (30,45) MK-NU-PK
The Advanced Power Booster Model PBIII (30,45) MK-NU-PK is an innovative, single-acting pump designed for the high-pressure feeding of both low and high-viscosity materials. This model is particularly effective for automatic applications, ensuring a constant and precise straight-line application when integrated with robotic systems. As part of ThreeBond’s suite of adhesive application equipments, the PBIII (30,45) MK-NU-PK enhances operational efficiency and accuracy, making it an essential tool for high-precision industrial processes.
Features:
- Dual Pump Ratio (30:1 or 45:1): Select the ideal pressure based on your material’s viscosity. This ensures smooth, consistent application without clogging or wasted material.
- Robotic Integration Ready: Seamlessly integrate the PBIII with your existing robotic systems. Together, they deliver precise, automated applications in straight lines, perfect for high-volume production.
- Space-Saving Design: Despite its power, the PBIII’s compact design maximizes your production floor efficiency.
- Safety Hand Switches: Prioritizing operator safety, the PBIII features built-in hand switches for complete control during operation.
- Built-in Material Saving Tank: Reduce material waste significantly with this innovative feature. By minimizing wasted sealant or adhesive, the PBIII translates to substantial cost savings over time.
Benefits:
High-Volume Production:
- Precision and Consistency: Maintain consistent, straight-line application for high-quality results, even in demanding production environments.
- Efficiency: Handle high-viscosity materials effectively, improving application speed and reducing downtime.
Focus on Material Savings:
- Material Savings: The PBIII’s material-saving tank significantly reduces waste, leading to substantial cost savings over time.
- Cost Recovery: The pump’s efficient operation and material-saving features can potentially pay for itself within 3-4 years!
General Application Needs:
- Safety and Reliability: Safety hand switches ensure safe operation, while the pump’s overall design guarantees reliable use in industrial environments.
- Economic Value: The PBIII offers a return on investment through material savings and potential cost recovery.
Beyond these core features and benefits, customization is key!
- Need even higher pressure? ThreeBond’s application experts can help you explore compatible high-pressure dispensing solutions.
- Unique Integration Needs? The PBIII can be adapted to work seamlessly with your existing robotic systems for a truly customized solution.
3. Single-Component Fixed-Quantity Booster Series
The Single-Component Fixed-Quantity Booster Series by ThreeBond is an advanced dispensing system designed for precision application of sealants and adhesives. This series is engineered to deliver a fixed volume of material through a consistent velocity drive mechanism powered by a stepping motor. As part of ThreeBond’s adhesive application equipments, this system allows for the precise numerical control of dispensing speed, ensuring high application accuracy and efficiency. This level of control and precision is essential for maintaining consistent quality and reducing material waste in industrial applications.
Features:
- Consistent Velocity Drive: This technology, powered by a stepping motor, ensures smooth and precise dispensing of a fixed volume of material. Every engine part receives the exact amount of sealant or adhesive needed.
- Numerical Speed Control: Fine-tune the dispensing speed with numerical controls. This allows for precise adjustments based on the specific material or application requirements, maximizing control and minimizing waste.
- Robotic Integration: Seamlessly integrate the booster with your existing robotic systems. Together, they enable automated application of a fixed quantity of material at a constant speed, ideal for high-volume production lines.
- LW Booster Integration (Optional): For enhanced quality control, the LW Booster can be integrated to maintain detailed records of sealant dispensing for each engine part. This valuable data stream allows for close monitoring and identification of any potential inconsistencies.
- High Application Quality: By ensuring even coverage and precise dispensing, the booster minimizes material waste and maintains consistent, high-quality results across every engine part.
Benefits Tailored to Your Needs:
Focus on Precision and Consistency:
- Precision and Consistency: Deliver the exact amount of material with each dispense, guaranteeing uniform application and minimizing the risk of errors in your engine assembly process.
- Ease of Adjustment: Fine-tune settings for optimal results based on the material and specific engine part requirements. This adaptability ensures consistent high quality.
Optimizing Material Usage:
- Material Savings: Accurate dispensing eliminates waste, reducing material usage and lowering your operational costs.
Boosting Automation and Quality Control:
- Enhanced Automation: Integrate the booster with robots to streamline dispensing processes and increase production efficiency on your engine assembly line.
- Improved Quality Control (with LW Booster): Gain valuable insights through detailed dispensing data for each engine part. This data allows for proactive monitoring and identification of any potential issues, ensuring consistent quality throughout your production process.
4. High-Viscosity Material Compatible Cartridge Pump (PCB-20)
The High-Viscosity Material Compatible Cartridge Pump (PCB-20) by ThreeBond is an advanced unit specifically designed for the high-pressure feeding of high-viscosity materials from cartridge containers to secondary discharge valves. As part of ThreeBond’s adhesive application equipments, this system ensures a uniform and precise linear application when the dispense valve is mounted onto a robotic system, making it ideal for demanding industrial applications. This high-precision setup is essential for industries that require consistent and accurate application of adhesives and sealants, ensuring efficiency and reliability in production processes.
Features:
- High-Pressure Feeding: The PCB-20 tackles even the most challenging high-viscosity materials with ease. Its efficient design ensures a consistent flow of material, eliminating inconsistencies and maintaining optimal pressure for precise application.
- Cartridge Compatibility: This pump is specifically designed to work seamlessly with cartridge containers. This allows for easy loading and unloading of materials, minimizing downtime and simplifying material handling processes.
- Robotic Integration: Ready to automate your dispensing? The PCB-20 integrates effortlessly with robotic systems. This powerful combination enables highly precise, uniform applications in straight lines – perfect for high-volume production environments.
- Consistent Application: Uniform dispensing is crucial for precision applications. The PCB-20 delivers consistent flow rates, ensuring each product receives the exact amount of material needed. This minimizes defects and the need for rework.
- Durability and Reliability: Built to handle the demands of high-viscosity materials, the PCB-20 is a dependable workhorse. Its robust design ensures long-lasting performance in even the most demanding industrial environments.
Benefits Tailored to Your Needs:
Focus on High-Quality Results:
- Precision and Uniformity: Achieve exceptional application quality with consistent flow rates. This reduces defects and the need for rework, leading to a flawless finished product.
Optimizing Efficiency and Productivity:
- Efficiency: The PCB-20’s efficient design minimizes material transfer losses and reduces downtime associated with material changes. This translates to increased productivity and overall efficiency.
- Ease of Use: Cartridge compatibility simplifies material loading and unloading, minimizing the risk of errors and operator training time.
Boosting Automation and Cost Savings:
- Enhanced Automation: Seamless robotic integration allows for automated dispensing, freeing up your workforce for higher-value tasks and significantly boosting production speed.
- Cost Savings: Reduced material waste and improved operational efficiency lead to substantial cost savings. The PCB-20 offers a significant return on investment (ROI) over time.
5. Automatic Robotic Sealant Dispensing Machines
ThreeBond’s Automatic Robotic Sealant Dispensing Machines are engineered for precision and efficiency in automotive sealing applications, particularly on engine flanges, transmissions, gears, and axles. As a part of ThreeBond’s adhesive application equipments, these advanced machines integrate cutting-edge technology to deliver accurate, consistent, and high-quality sealant application, making them a critical asset for major automotive manufacturers worldwide. Their ability to optimize sealant usage and enhance application precision ensures superior performance and reliability in automotive components, significantly benefiting the manufacturing process.
Features:
- Accurate Application: The core of the system ensures precise bead placement, critical for creating perfect seals on vital automotive components. This translates to optimal performance and extended component lifespan.
- Material Savings: Minimize sealant waste with controlled application. This not only reduces material costs but also minimizes environmental impact.
- Multi-Component Capability: Handle sealing applications for multiple engine, transmission, gear & axle components within a single machine. This streamlines operations and boosts production efficiency.
- Optional Laser Sensor: For the most demanding applications, integrate a laser sensor for real-time monitoring of bead size. This advanced feature ensures consistent and precise application, eliminating potential inconsistencies.
- Easy-to-Use Operator Panel: The user-friendly interface allows for simple programming and operation. This reduces training time and the risk of errors, even for new operators.
- Optional Vision Camera System (For Advanced Needs): For even greater control, consider integrating a vision camera system. This advanced feature allows for real-time monitoring of not only bead size but also the overall bead profile. This ensures perfect and consistent seals, crucial for mission-critical components.
- Easy Maintenance & Handling: The machine’s design prioritizes user-friendliness. Simplified maintenance and operation minimize downtime and associated costs.
Benefits Tailored to Your Needs:
- Enhanced Precision (with Laser Sensor): Achieve perfect seals on every engine, transmission, gear & axle component, ensuring optimal performance and longevity. The optional laser sensor offers an extra layer of control for the most demanding applications.
- Cost Efficiency: Minimize sealant waste and optimize material use for substantial cost savings.
- Operational Flexibility: Handle sealing for multiple components with a single machine, streamlining your production processes.
- Reduced Defects: Consistent application minimizes defects and the need for rework, leading to higher quality output.
- User-Friendly: Simple programming and operation reduce training time and minimize errors.
- Advanced Monitoring (Optional): Gain real-time insights into both bead size and profile with optional sensor integration. This ensures consistent application and adherence to the highest quality standards.
- Long-Term Reliability: Durable construction and simplified maintenance minimize downtime and keep your production lines running smoothly.
6. Various Other Small Dispensing Equipment
ThreeBond has developed an array of small dispensing equipment designed to enhance efficiency and optimize the use of their liquid gasket, locking agent, adhesive, sealant, and other products. As part of ThreeBond’s adhesive application equipments, these tools are engineered to save labor, reduce waste, and improve application precision, ensuring users can apply ThreeBond’s products effectively and rationally. Here is an overview of these innovative dispensing solutions:
Features
- Labor-Saving Design
- Description: These tools are designed to reduce the manual effort required in application processes.
- Application: Streamlines the dispensing of materials, making the process quicker and less labor-intensive.
- Versatile Applications
- Description: Suitable for use with liquid gaskets, locking agents, adhesives, and sealants.
- Application: Provides flexibility in various industrial uses, accommodating different types of ThreeBond products.
- Precision Dispensing
- Description: Ensures accurate and consistent application of materials.
- Application: Reduces the risk of over-application and waste, ensuring that the right amount of material is applied every time.
- Compact and Ergonomic
- Description: Small, user-friendly designs.
- Application: Easy to handle and integrate into existing workflows, minimizing space requirements and enhancing usability.
- Durable Construction
- Description: Built to withstand rigorous industrial use.
- Application: Ensures longevity and reliability, even in demanding environments.
- Easy Maintenance
- Description: Simplified maintenance procedures.
- Application: Reduces downtime and ensures continuous operation, making maintenance straightforward and less time-consuming.
Benefits
- Increased Efficiency
- Advantage: Speeds up application processes.
- Result: Allows for quicker turnaround times and higher productivity, enhancing overall operational efficiency.
- Material Savings
- Advantage: Reduces material waste.
- Result: Leads to significant cost savings by ensuring that only the necessary amount of material is used, reducing excess and waste.
- Improved Application Quality
- Advantage: Ensures high-quality results.
- Result: Enhances the performance and durability of the applied products, contributing to better end-product quality.
- User-Friendly
- Advantage: Easy to use.
- Result: Reduces operator fatigue and minimizes the need for extensive training, making the equipment accessible to all operators.
- Long-Term Reliability
- Advantage: Durable and easy to maintain.
- Result: Minimizes the need for frequent replacements or repairs, ensuring that the equipment remains functional and reliable over long periods.
- Adaptability
- Advantage: Compatible with a wide range of ThreeBond products.
- Result: Provides a comprehensive solution for various application needs, making the equipment versatile and useful in multiple scenarios.
Why Choose ThreeBond’s Adhesive Application Equipments?
ThreeBond’s tools ensure consistent quality, save materials, and enhance efficiency in adhesive and sealant applications. Whether for automotive, industrial, or general use, these advanced solutions represent a technological leap in application precision.
Conclusion
Investing in ThreeBond’s adhesive application equipments means optimizing your adhesive and sealant processes for better performance and cost savings. Discover the range today and take your applications to the next level. ThreeBond’s range of adhesive application equipments offers unparalleled precision, efficiency, and cost savings for industrial adhesive and sealant applications. By investing in these cutting-edge tools, businesses can optimize their processes, improve application quality, and enhance overall operational efficiency. With ThreeBond’s advanced solutions, organizations can take their adhesive and sealant applications to the next level, ensuring consistent quality and substantial material savings. Explore ThreeBond’s adhesive application equipments today and revolutionize your application processes for superior results.
Post a comment