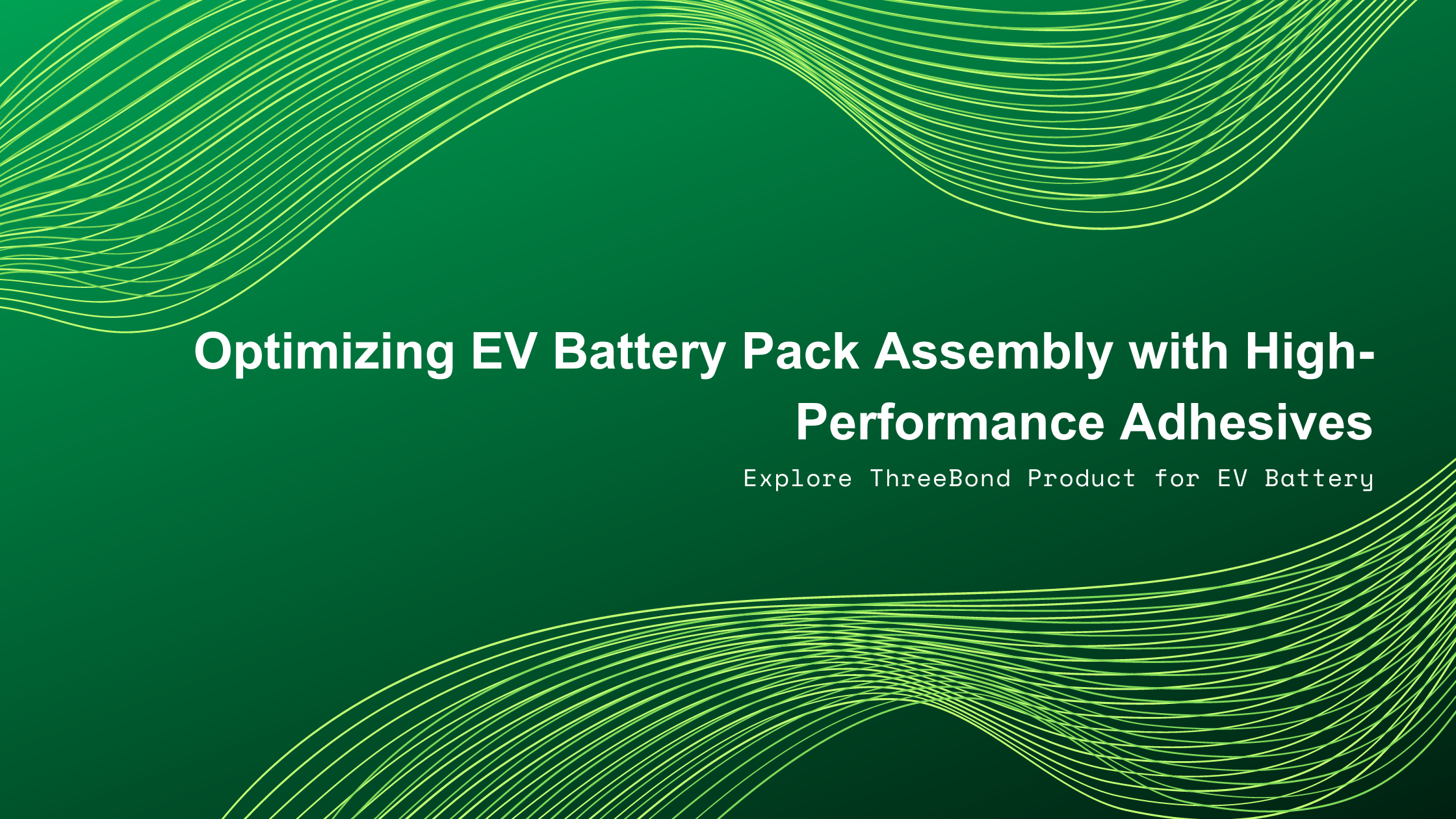
Optimizing EV Battery Pack Assembly with High-Performance Adhesives
As electric vehicles (EVs) grow in prevalence on our streets, the technology used to create their batteries keeps changing. The assembly process is a vital part of the design and manufacture of EV batteries. It is in this blog that we will find out about how these adhesives enhance EV battery pack assembly, improve thermal management, sustain the environment, and contribute to structural integrity.
Introduction
With sustainability as the global focus, there has been an astronomical surge in demand for Electric Vehicles (EVs), signaling a transformative shift in the automotive industry as it stands today. Battery pack assembly is central to EV manufacturing, where intelligent use of high-performance adhesives is indispensable.
Understanding EV Battery Pack Assembly
But before we look at this role of adhesives, let’s first understand how an EV battery pack is put together. An electric vehicle battery pack consists of multiple battery cells packed into modules or packs, which are then integrated into the vehicle frame. The production method must ensure that appropriate attention to detail is provided for structural integrity, overall performance, and thermal management during this process.
Components that make up an EV Battery Pack
EV battery packs are intricate assemblies of various components:
- Cells: These form the basic units responsible for storing electrical energy.
- Module: Clusters of cells organized for efficiency and space optimization.
- Pack: The final enclosure contains multiple modules which are sealed to ensure safety and integration.
Challenges in Battery Pack Assembly
Battery pack assembly is met with several challenges:
- Thermal Management: Efficient heat dissipation is crucial to maintain battery performance and longevity.
- Vibration & Mechanical Stress: Preventing structural damage from vibrations and mechanical forces is essential.
- Weight Reduction: Strive to reduce pack weight without compromising strength or safety.
- Electrical Insulation: Ensure insulation against short circuits and electrical hazards.
The Role of Adhesives in the Assembly of Battery Packs
These difficulties are why high-performance adhesives have become such linchpins. By forming strong, durable bonds that connect many parts together, this adhesive helps to maintain the battery’s structure, manages heat well, reduces vibrations, and makes the battery light.
Benefits of High-Performance Adhesives in the EV Battery Manufacturing Process
- Higher Bonding Strength: Makes sure there is a brutal bond amidst components, increasing their lifespan and efficiency.
- Better Heat Conductivity: Ensures efficient heat flow through, which prevents overheating and extends battery life.
- Reducing Vibrations and Mechanical Stability: This leads to decreased shaking while also making equipment more stable, thereby reducing chances for breakdowns.
- Weight Losing and Constructional Integrity: Which can be achieved thanks to reduced weight without affecting structural integrity features like strength?
- Thermal management and Electric Insulation: It provides insulation against electricity and helps control temperature variations, hence guaranteeing the safety of operations.
Pertinent Guidelines for Choosing High-Performance Adhesives
- Battery Material Compatibility: in order to achieve proper functioning, adhesives should be compatible with battery materials.
- Resistance to Temperature Change: they must not lose their sticking power even if subjected to extreme temperatures.
- Time Taken to Cure and Processability: the time it takes to dry out an adhesive speeds up production, whereas simplicity of use makes a product more processable.
- Longevity and Dependability Issues Over a Long Term: In particular, the adhesive must serve as a long-term protector against strain experienced by electric vehicles (EVs).
- Compliance with Regulatory Standards and Safety Requirements: To ensure user safety and adherence, such adhesives are expected to conform to existing rules.
ThreeBond Product for EV Battery
ThreeBond 1160:
Non-silicone sealant for automotive electronics and EV battery packs.
- Formulation: Silyl-based, with high-performance capabilities.
- Appearance: Black, indicating strength and durability.
- Viscosity: 125 Pa・s, facilitating easy application and precise dispensing.
- Strength: Tensile strength of 2.0 MPa and 460% elongation for robust bonding.
- Reliability: Withstands rigorous heat and humidity resistance tests.
- Compliance: Meets export regulations in the EU, China, Korea, and the USA.
- Benefits: Superior to rubber gaskets, enabling efficient assembly and ensuring structural integrity.
ThreeBond 2045B and ThreeBond 2145B:
Epoxy-based adhesives are designed for heat dissipation in battery cells.
- Features: High tensile shear bond strength for secure bonding between materials like steel, aluminum, copper, and nickel.
- Performance: It withstands high temperatures and humid conditions and is suitable for demanding applications.
- Thermal Conductivity: Remarkable 2.1 W/m・K, equivalent to UL94 V-0 standards, ensuring excellent heat dissipation.
- Cure: Cures at room temperature without additional heating facilities, enhancing convenience in manufacturing processes.
- Overall: Offers exceptional adhesive strength and thermal performance, ideal for heat management in battery cell assemblies.
ThreeBond 3953:
TB3953 is a robust, two-part adhesive renowned for its exceptional bonding capabilities. It is set at room temperature without requiring additional equipment, and it’s eco-friendly, complying with EU regulations. With a tensile shear bond strength of 15 MPa, it’s ideal for affixing items like battery cells. Its heat and humidity resistance ensure reliability even under harsh conditions. Key features include:
- Strong adhesion to various materials.
- Versatility for automotive and industrial uses.
- Offers elasticity and high strength, akin to a stretchy rubber.
- Superior sealing properties, perfect for high-pressure hydrogen tanks.
- User-friendly application with a 1:1 mixing ratio and a 15-20 minute pot life.
- Multiple applications beyond automotive, including in drones, signage, and marine contexts.
Technical specifications:
- Appearance: Black (leading agent) and white (curing agent).
- Viscosity: Suitable consistency for easy handling.
- Specific Gravity: Indicates density compared to water.
- Gel Time: The time it takes to thicken after mixing.
- Packaging: Comes in a twin cartridge for convenient dispensing.
- Volume: Each cartridge contains 46 ml.
- Shelf Life: Lasts approximately 5 months when stored between -5°C to 40°C.
ThreeBond 3380:
TB3380: Two-component epoxy-based conductive adhesive.
- Application: Used for grounding in batteries.
- Curing: Room temperature curing; no special conditions are required.
- Appearance: Black, blends well with surfaces.
- Properties: Offers good connection resistance and adhesion to various materials.
- Specific Gravity: Ranges from 3.1 to 3.3.
- Viscosity: 200 to 250 Pa・s, easy to apply.
- Mixing Ratio: 100:100 by weight.
- Pot Life: Approximately 60 minutes.
- Shrinkage: Minimal at 2.8% upon curing.
- Bond Strength: Tensile shear bond strength of 6.0 MPa.
- Substrates: Reliable bonding to aluminum substrates (Al/A(l A1050P)).
- Summary: Convenient and effective solution for grounding applications, boasting strong adhesion properties.
You Need to Read This: The Role of Adhesives in Securing and Protecting EV Batteries.
EV Battery Assembly Applications of High-performance Adhesives
High-performance adhesives find use in a number of battery assembly stages:
- Cell-to-cell Bonding: Creating solid connections among each cell of the batteries.
- Module Assembly: Adhesion of the cells to form modules that can be easily incorporated into the system.
- Pack Encapsulation and Sealing: This creates an airtight seal around battery packs, thus protecting them from external factors.
- Busbar Attachment: Solvent bonding is used for fast and efficient current transmission within battery packs.
- Thermal Interface Materials (TIMs): These help in conducting heat between battery cells and coolers.
Case Studies: Successful Implementation of High-Performance Adhesives
EV battery assembly may begin with the use of high-performance adhesives, as evidenced by some case studies:
- Automaker OEM Case Study: Streamlined production and increased efficiency are demonstrated using adhesive bonding.
- Battery Maker Case Study: Use of high-performance adhesives to increase performance and reliability.
- Research Institute Case Study: Highlighting innovations in battery assembly techniques due to advanced adhesive technology.
Latest Developments in High-Performance Adhesives for EV Battery Assembly
Continuous improvements have been observed in EV battery assembly due to ongoing developments in adhesive technology:
- Improved Thermal Management Utilizing Advanced Formulations: Heat dissipation is enhanced by better thermal conductivity of adhesives.
- Novel Adhesive Technologies that Enhance Electrical Insulation: Adhesion that isolates electrically, thus preventing short circuits, was improved upon in composite materials.
- Sustainable and Eco-Friendly Adhesive Solutions: Environmentally friendly formulations and manufacturing processes are used.
- Integration of Smart Adhesives for Real-Time Monitoring: Designers are using innovative adhesives that contain sensors to monitor the state of health/performance of batteries.
Best Practices for the Use of High-Performance Adhesives in EV Battery Assembly
Adherence to best practices ensures the successful implementation of high-performance adhesives:
- Proper Surface Preparation and Cleaning: This ensures clean surfaces, which leads to optimal adhesive bonding.
- Precise Dispensing and Application Techniques: The use of accurate dispensing methods can help reduce wastage.
- Controlled Curing Conditions and Quality Assurance: These practices include maintaining controlled conditions as well as firm quality assurance measures.
- Training and Education for Assembly Personnel: It is necessary to have comprehensive training so that adhesives can be handled properly while applying them.
- Continuous Monitoring and Maintenance Practices: Regular monitoring, together with maintenance practices, should be done so that issues on adhesives are dealt with immediately.
Future Trends and Opportunities in EV Battery Pack Assembly
The future of EV battery pack assembly holds exciting prospects:
- Advancements in materials science and adhesive technology: Developing a new material to correspond with changing performance requirements.
- Integration of artificial intelligence and automation: Utilizing AI and automation to increase accuracy and efficiency.
- Collaborative R&D initiatives for industry innovation: Industry-wide Innovations through collaboration across sectors
- Market Expansion and Global Adoption of Electric Vehicles: Entering new markets and regions as demand for EVs grows
Conclusion
In conclusion, high-performance adhesives play a critical role in the development of optimized EV battery pack assembly, as they provide multiple benefits, from stronger bonding to improved temperature control. The correct selection of adhesives can make mass production of sustainable batteries reliable, efficient, and achievable, thus aiding in environmentally friendly mobility through electric vehicles.
Post a comment