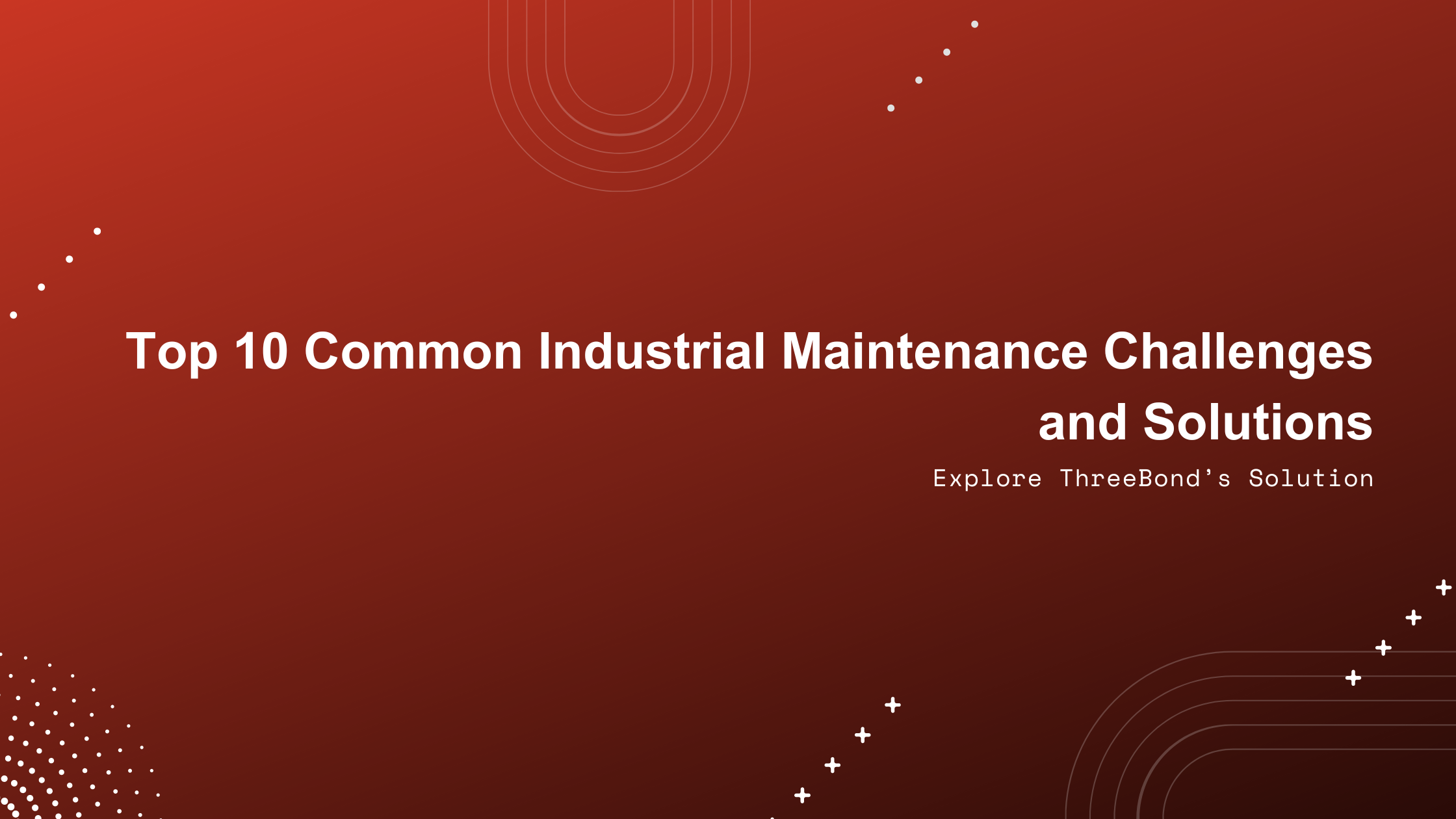
Top 10 Common Industrial Maintenance Challenges and Solutions
Industrial maintenance is crucial for ensuring the smooth operation of machinery, equipment, and facilities within industrial settings. However, maintenance teams often face various challenges that can impact productivity, safety, and profitability. In this blog, we’ll explore the top 10 common industrial maintenance challenges and provide practical solutions to address them effectively.
Here are 10 industrial maintenance challenges and solutions
Lack of Standards
Challenge: Maintenance procedures often lack standardization in the industrial maintenance sector, leading to ambiguity and inefficiency. Technicians may struggle to follow inconsistent processes, resulting in wasted time and increased risk of errors.
Solution: Implement standardized operating procedures (SOPs) that clearly define industrial maintenance tasks, schedules, and protocols. Host SOPs on a central repository like a mobile CMMS for easy access and adherence.
ThreeBond’s Standards
Three Bond, a renowned global leader in Sealants, Adhesives, and other essential engineering products, upholds rigorous product standards to ensure the highest quality and performance across its diverse range of offerings. These product standards encompass various aspects, including formulation, manufacturing processes, testing procedures, and compliance with industry regulations. Here are Three Bond’s product standards:
1. Formulation Excellence
Three Bond employs advanced tech and research to formulate high-performing products. Selection of materials for optimal properties. Rigorous testing ensures adherence to quality standards and performance needs.
2. Manufacturing Precision
ThreeBond utilizes advanced facilities and automation for precise manufacturing. Stringent quality control monitors parameters like temperature and pressure. Skilled technicians uphold quality standards and adhere to specifications during production.
3. Testing and Validation
ThreeBond products undergo thorough testing for mechanical, durability, chemical, and thermal properties. Laboratory tests, aging studies, and simulations ensure reliability and suitability for intended applications. They comply with industry certifications.
4. Compliance and Certification
ThreeBond products meet industry standards and regulations, adhering to ISO quality management systems for consistency and environmental responsibility.
5. Continuous Improvement
ThreeBond prioritizes continuous improvement, driven by customer feedback, market trends, and technological advancements. Investments in research, training, and collaboration aim to enhance product performance and meet evolving customer needs.
In summary, ThreeBond’s product standards prioritize quality, reliability, and customer satisfaction. Upholding rigorous standards in formulation, manufacturing, testing, compliance, and continuous improvement ensures exceptional performance.
Unplanned Downtime
Challenge: Unexpected machine failures can cause disruptions in plant operations, resulting in downtime and productivity losses. Traditional reactive maintenance approaches may not effectively prevent unplanned downtime. Industrial maintenance strategies need to evolve to incorporate proactive measures that can identify and address potential issues before they escalate into costly breakdowns.
Solution: Adopt predictive maintenance strategies leveraging Industry 4.0 technologies. Monitor equipment health in real-time using sensors and predictive analytics to anticipate failures and schedule proactive maintenance interventions.
Tight Maintenance Budgets
Challenge: Limited resources allocated for maintenance activities can hinder the implementation of comprehensive maintenance programs. Balancing maintenance needs with budget constraints is a common struggle for maintenance managers.
Solution: Focus on preventive maintenance to optimize resources and minimize costly unplanned repairs. Present the business case for effective maintenance to management, emphasizing the long-term cost savings and operational benefits.
Three Bond India’s Solution Products for Tight Maintenance Budgets
In response to the common struggle faced by maintenance managers dealing with limited resources, ThreeBond India presents a range of innovative solutions tailored to optimize maintenance activities within tight budgets. Our products are designed to address the challenges of balancing maintenance needs with financial constraints while ensuring operational efficiency and longevity of equipment.
Three Bond Maintenance Coatings
Our specialized maintenance coatings offer a proactive approach to equipment care, providing durable protection against wear, corrosion, and environmental factors. By applying these coatings preventively, maintenance managers can extend the lifespan of critical assets, reducing the frequency of repairs and associated costs.
ThreeBond Sealants and Adhesives
Leaks and failures in machinery can lead to costly downtime and repairs. Our high-performance sealants and adhesives provide reliable sealing solutions for various applications, helping to prevent leaks and maintain equipment integrity. By addressing potential issues proactively, maintenance teams can minimize the risk of unplanned breakdowns and the associated expenses.
ThreeBond Lubricants
Proper lubrication is essential for the smooth operation of machinery, reducing friction, wear, and energy consumption. Our range of lubricants is formulated to optimize equipment performance and longevity, even under demanding operating conditions. By implementing a proactive lubrication schedule using ThreeBond lubricants, maintenance managers can minimize the risk of equipment failure and extend maintenance intervals, maximizing the efficiency of their maintenance budget.
ThreeBond India’s solution products for tight maintenance budgets, maintenance managers can shift towards a preventive maintenance approach that emphasizes cost-effectiveness and operational reliability. These products not only help to optimize resources but also contribute to long-term cost savings and enhanced equipment performance, ultimately driving business success.
Skilled Workforce Shortage
Challenge: Finding and retaining skilled maintenance technicians is a persistent challenge in the industrial sector. The demand for qualified personnel often exceeds the available supply, leading to talent shortages.
Solution: Invest in recruitment efforts, training programs, and career development opportunities to attract and retain skilled technicians. Collaborate with technical schools and vocational training programs to bridge the skills gap and develop a pipeline of talent.
Aging Infrastructure and Equipment
Challenge: Aging equipment and infrastructure are more prone to failures, requiring increased attention and maintenance. Outdated equipment may lack efficiency and reliability, posing risks to operations.
Solution: Implement condition-based maintenance strategies to monitor the health of aging equipment and prioritize maintenance activities based on criticality and risk. Consider modernization initiatives and equipment upgrades to enhance reliability and efficiency.
Lack of Collaboration and Communication
Challenge: Poor collaboration and communication between maintenance teams and other departments can lead to inefficiencies, misunderstandings, and delays in addressing maintenance issues.
Solution: Foster a culture of collaboration and open communication within the organization. Encourage cross-functional teamwork between maintenance, operations, and management to align goals and share information effectively.
Inadequate Maintenance Documentation
Challenge: Incomplete or outdated maintenance documentation can hinder the effectiveness of maintenance programs and lead to compliance issues. Without proper documentation, it’s challenging to track maintenance history and make data-driven decisions.
Solution: Implement a robust maintenance tracking system such as a computerized maintenance management system (CMMS) to streamline documentation processes. Maintain comprehensive records of maintenance activities, equipment specifications, and inspection reports for compliance and analysis purposes.
Safety Concerns
Challenge: Safety hazards resulting from equipment failures or maintenance activities pose risks to personnel and plant operations. Failure to prioritize safety can lead to accidents, injuries, and regulatory violations.
Solution: Prioritize safety in all maintenance activities and adhere to established safety protocols and regulations. Conduct regular safety inspections, provide safety training to personnel, and promote a safety-first culture throughout the organization.
Complex Regulatory Compliance
Challenge: Industrial maintenance operations must comply with a myriad of regulations and standards governing safety, environmental protection, and equipment maintenance. Keeping up with changing regulations can be overwhelming.
Solution: Stay informed about regulatory requirements relevant to industrial maintenance operations and ensure compliance through proactive measures. Establish internal protocols and procedures to address regulatory requirements effectively and mitigate compliance risks.
Resistance to Change
Challenge: Resistance to change within the organization can hinder the adoption of new maintenance practices, technologies, or processes. Employees may be reluctant to embrace change due to fear of the unknown or perceived disruptions.
Solution: Foster a culture of continuous improvement and innovation within the organization. Provide training and support to employees to help them adapt to new maintenance practices and technologies. Communicate the benefits of change and involve employees in the decision-making process to gain buy-in and support.
Conclusion
Effective industrial maintenance is essential for ensuring the reliability, efficiency, and safety of industrial operations. By addressing common maintenance challenges with practical solutions, organizations can optimize maintenance processes, minimize downtime, and maximize productivity. By fostering collaboration, embracing innovation, and prioritizing safety, organizations can overcome challenges and achieve sustainable success in industrial maintenance.
Post a comment