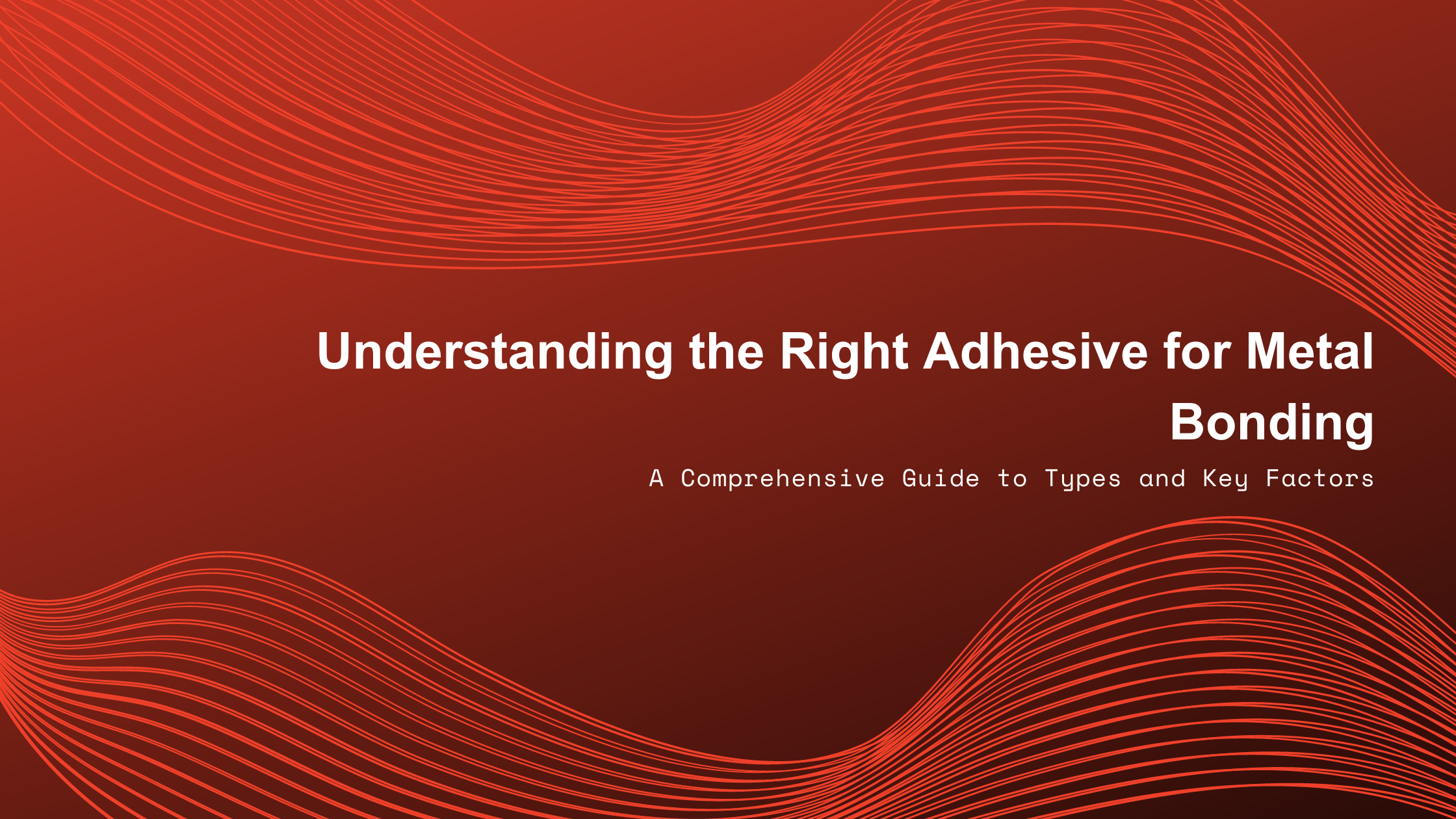
Understanding the Right Adhesive for Metal Bonding: A Comprehensive Guide to Types and Key Factors
When it comes to metal bonding, the choice of adhesive can significantly impact the strength, durability, and longevity of the bond. Whether you are a DIY enthusiast or a professional in the manufacturing industry, understanding the various adhesives for metal bonding is crucial for achieving successful results. This comprehensive guide will explore the different types of adhesives available for metal bonding, key factors to consider when selecting an adhesive, and best practices for effective application.
The Importance of Adhesives for Metal Bonding
Adhesives have become increasingly popular in metal bonding applications due to their ability to create strong joints without the need for heat. Unlike welding or soldering, which can alter the properties of metals, adhesives for metal bonding provide a versatile solution that can be used in various environments. They are commonly employed in industries ranging from automotive to aerospace, where reliability and performance are paramount.
Advantages of Using Adhesives for Metal Bonding
- No Heat Required: Many adhesives for metal bonding work effectively at room temperature, eliminating the risks associated with heat distortion.
- Flexibility: Adhesives can accommodate movement and vibrations better than rigid joints created by welding or mechanical fasteners.
- Ease of Application: Most adhesives are user-friendly and require minimal equipment.
- Cost-Effectiveness: Adhesives often provide a more economical solution compared to traditional fastening methods.
Types of Adhesives for Metal Bonding
Choosing the right adhesive depends on several factors, including the type of metal being bonded, environmental conditions, and specific project requirements. Here are some common types of adhesives for metal bonding:
1. Epoxy Adhesives
Epoxy adhesives are two-component systems consisting of a resin and a hardener. When mixed, they create a strong bond that is resistant to heat and chemicals.
- Advantages:
- High strength and durability
- Excellent resistance to heat and chemicals
- Suitable for bonding various metals, including steel and aluminum
- Disadvantages:
- Longer curing time (typically 24 hours)
- Requires surface preparation for optimal adhesion
2. Cyanoacrylate Adhesives (Super Glue)
Cyanoacrylate adhesives are known for their fast-drying properties and strong bond formation upon exposure to moisture.
- Advantages:
- Quick setting time (seconds to minutes)
- Ideal for small metal parts
- Dries clear, making it aesthetically pleasing
- Disadvantages:
- Limited gap-filling capabilities
- Not suitable for load-bearing applications
3. Polyurethane Adhesives
Polyurethane adhesives are versatile and flexible, making them suitable for applications where movement or vibration is expected.
- Advantages:
- Strong bond with good flexibility
- Resistant to moisture and chemicals
- Suitable for outdoor applications
- Disadvantages:
- Longer curing time compared to other adhesives
- May require clamping during curing
Real Also: The Ultimate Guide to Adhesives: Types, Uses, and Tips.
4. Methyl Methacrylate (MMA) Adhesives
MMA adhesives provide excellent tensile strength and are engineered for high-performance applications.
- Advantages:
- Fast setting times
- Strong resistance to impact and environmental conditions
- Disadvantages:
- Requires careful handling due to rapid curing
The following adhesives from ThreeBond are suitable for metal bonding:
- ThreeBond 1521 (Multi-Purpose Rubber Adhesive)
- Application: Effective for metal surfaces, especially after proper surface preparation, such as removing rust and oxide films.
- ThreeBond 1530 (Single-Component, Moisture Cure Type Elastic Adhesive)
- Application: Bonds well with metal and is suitable for various materials including rubber and wood.
- ThreeBond 1741 (Cyanoacrylate-Based Instant High-Strength Adhesive)
- Application: Strong adhesion to metal, ceramics, rubber, and plastic; ideal for quick fixes.
- ThreeBond 1743 (Cyanoacrylate-Based Instant High-Strength Adhesive)
- Application: Similar to 1741, it bonds well with metal and is suitable for various materials.
- ThreeBond 1747 (Cyanoacrylate-Based Instant High-Strength Adhesive)
- Application: Excellent adhesion to difficult surfaces, including metals, with quick curing time.
- ThreeBond 1782 (Cyanoacrylate-Based Instant Adhesive)
- Application: Suitable for automotive components and electronic products that require heat and impact resistance.
- ThreeBond 3013B (Solvent-Free UV Curable Adhesive)
- Application: Excellent adhesion to various substrates, including metals, when cured under UV light.
- ThreeBond 3921 and ThreeBond 3926 (Two-Component Acrylic Structural Adhesive)
- Application: Bonds different types of metals effectively and provides good initial strength.
- ThreeBond 3732
- Application: Suitable for bonding ceramic, glass, or metal; offers good water resistance and sealing ability.
To know about Heat Dissipation, Read this blog: Heat Dissipation Explained: The Science and Formula Behind Efficient Cooling.
Key Factors to Consider When Choosing Adhesives for Metal Bonding
Selecting the right adhesive involves considering several key factors that can impact the effectiveness of the bond:
Metal Type
Different metals react differently with adhesives. For example:
- Aluminum: Requires careful surface preparation due to its oxide layer.
- Stainless Steel: Can be bonded effectively with most adhesives but may require a primer.
- Copper: Often requires specialized adhesives due to its high thermal conductivity.
Environmental Conditions
Consider where the bonded materials will be used:
- Temperature Extremes: Some adhesives perform better in high or low temperatures.
- Moisture Exposure: If the bond will be exposed to water or humidity, choose a moisture-resistant adhesive.
Load Requirements
Determine whether the bond will need to support weight or withstand stress. For heavy-duty applications, stronger adhesives like epoxies or MMAs may be necessary.
Curing Time
Depending on your project timeline, you may need an adhesive with a quick curing time or one that allows more working time before setting.
Best Practices for Using Adhesives for Metal Bonding
Achieving a strong bond requires more than just selecting the right adhesive; proper preparation and application techniques are essential.
Surface Preparation
- Cleaning: Remove dirt, grease, rust, or any contaminants from the metal surfaces using a degreaser or solvent.
- Sanding: Lightly sand both surfaces with fine-grit sandpaper to create a rough texture that enhances adhesion.
- Priming (if necessary): Some metals may benefit from a primer that improves adhesion between the adhesive and metal surface.
Applying the Adhesive
- Mixing (for two-part systems): Follow manufacturer instructions carefully when mixing epoxies or other two-component adhesives.
- Application Method: Use an applicator nozzle or brush to apply an even layer of adhesive on one surface.
- Joining Surfaces: Align the two metal pieces carefully before pressing them together. Avoid excessive movement once they are joined.
Clamping and Curing
- Clamping: Use clamps or weights to hold the pieces together during curing, ensuring even pressure across the bond.
- Curing Time: Allow adequate time for curing as specified by the adhesive manufacturer—typically at least 24 hours before applying stress.
Common Mistakes to Avoid When Using Adhesives for Metal Bonding
- Inadequate Surface Preparation: Failing to clean or sand surfaces can lead to weak bonds.
- Using Incorrect Adhesive: Not considering metal type or environmental factors can result in bond failure.
- Ignoring Curing Times: Rushing the process can compromise bond strength; always adhere to recommended curing times.
Conclusion
Understanding how to choose and apply adhesives for metal bonding is crucial for achieving strong, durable connections in various projects. By considering factors such as metal type, environmental conditions, load requirements, and following best practices for preparation and application, you can ensure successful bonding outcomes.
Whether you’re tackling a DIY project at home or working on industrial applications, this comprehensive guide provides you with the knowledge needed to select the right adhesive for your metal bonding needs. With patience and attention to detail, you can master the art of metal adhesion and achieve professional results in your projects.
In summary, when it comes to selecting adhesives for metal bonding, remember that each type has its unique advantages and disadvantages. Understanding these differences will empower you to make informed choices that lead to successful outcomes in your projects. Whether you opt for epoxy, cyanoacrylate, polyurethane, or MMA adhesives, following proper techniques will ensure that your bonds remain strong over time.
Post a comment