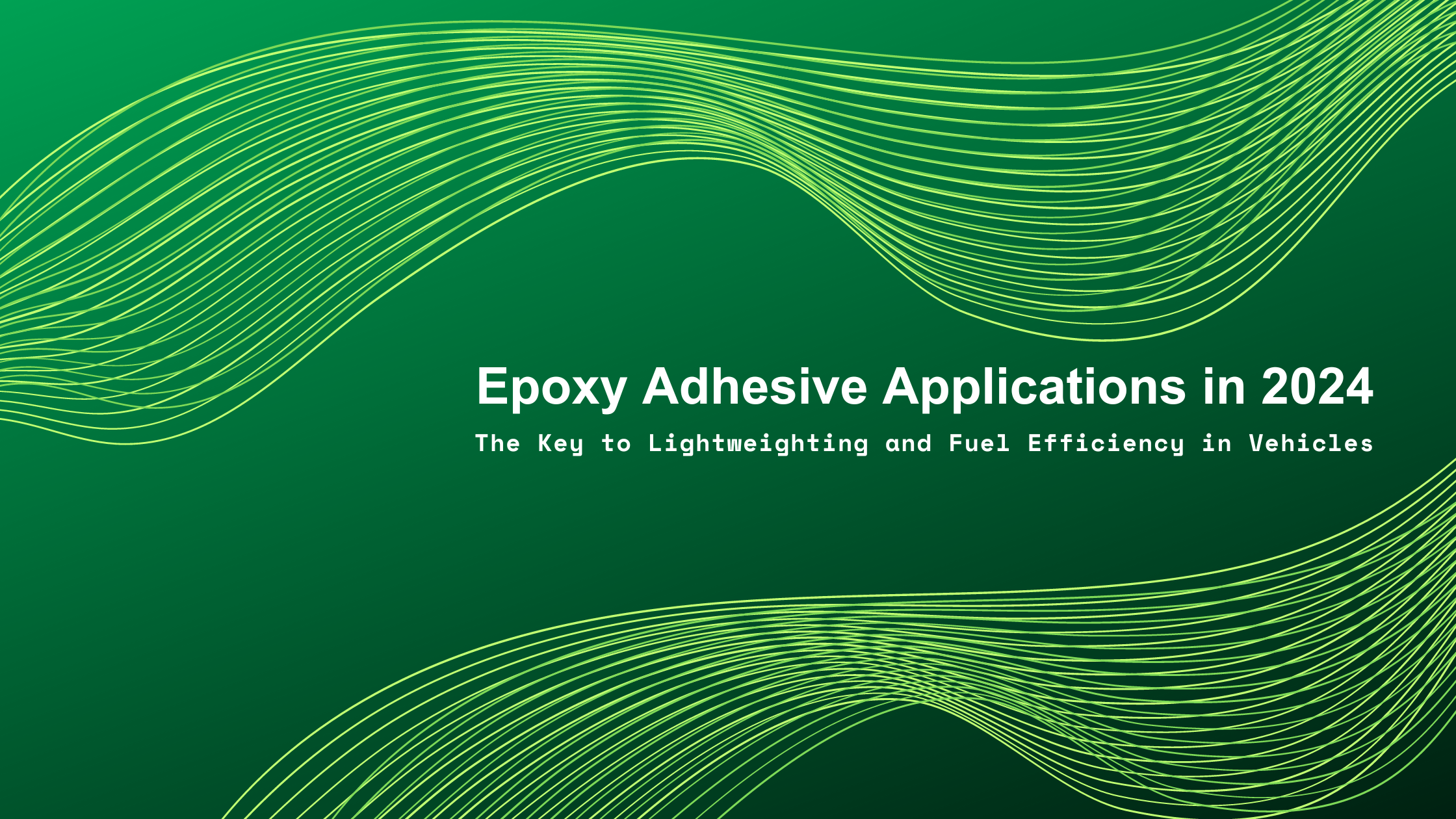
Adhesive Applications in 2024: The Key to Lightweighting and Fuel Efficiency in Vehicles
In the world of automotive innovation, one key player often goes unnoticed but plays a crucial role in making vehicles lighter, more efficient, and safer: adhesive. As we step into 2024, the significance of adhesives applications in the automotive industry has only grown, paving the way for groundbreaking advancements in vehicle design and performance.
What exactly are adhesives, what are their applications, and why are they so important? Let’s dive into the world of adhesives and explore their transformative impact on the automotive landscape.
Understanding Adhesive Applications
Adhesives applications refer to the use of adhesives in various aspects of vehicle manufacturing and assembly. These adhesives, made from a curing agent, offer exceptional bonding strength and versatility, making them ideal for joining different materials together.
The Role of Adhesives in Lightweighting
In an era where fuel efficiency and sustainability are top priorities, lightweighting has become a primary focus for automotive manufacturers. Adhesives play a crucial role in this process by enabling the use of lightweight materials such as carbon fiber, aluminum, and advanced composites.
By bonding these lightweight materials together with adhesives, manufacturers can reduce the overall weight of vehicles without compromising structural integrity or safety. This, in turn, leads to improved fuel efficiency, reduced emissions, and enhanced performance.
Fuel Efficiency and Performance Enhancement
Adhesive applications contribute to more than just lightweighting; they also play a significant role in enhancing fuel efficiency and vehicle performance. By reducing the weight of vehicles, adhesives help optimize power-to-weight ratios, resulting in better acceleration, handling, and overall driving dynamics.
Moreover, the use of adhesives allows for more streamlined and aerodynamic designs, further improving fuel efficiency by reducing drag and optimizing airflow. This combination of lightweighting and aerodynamic optimization makes vehicles more fuel-efficient and environmentally friendly.
Safety and Structural Integrity
Beyond lightweighting and fuel efficiency, adhesive applications also enhance safety and structural integrity in vehicles. These adhesives create strong and durable bonds between different components, forming a unified structure that can withstand various stresses and forces encountered during operation.
In the event of a collision, bonded structures exhibit excellent crash performance, absorbing energy and minimizing deformation to protect occupants. Additionally, the use of adhesives in structural bonding reduces noise, vibration, and harshness (NVH), leading to a quieter and more comfortable driving experience.
You need to read this: Transforming Mobility: The Impact of Epoxy Adhesive Technology on Electric Motor Performance.
Future Trends in Adhesive Applications
In the future, Adhesive applications in the automotive industry hold immense promise. Emerging technologies like nanomaterials, bio-based resins, and additive manufacturing are poised to revolutionize efforts in lightweighting and fuel efficiency. Innovations in adhesives formulations, including self-healing properties and multifunctional capabilities, will further enhance the performance and sustainability of future vehicles.
Looking ahead, various trends and innovations are shaping the future of adhesives applications in the automotive industry. Advances in adhesive technology, such as the development of high-strength and fast-curing formulations, enable greater integration of lightweight materials and complex structures in vehicles.
Moreover, the emergence of electric and autonomous vehicles creates new opportunities for adhesive applications. Electric vehicles benefit from lightweighting to extend range and battery life, while autonomous vehicles require robust bonding solutions for sensor integration and structural rigidity.
ThreeBond Products
ThreeBond 3921 / ThreeBond 3926
ThreeBond 3921 and ThreeBond 3926 are strong adhesives used in making cars, ships, and buildings. They stick quickly, making assembly faster. They work well on metals and plastics, are tough against breaking and peeling, and don’t smell bad. They’re like superglue for big things!
ThreeBond 3955
ThreeBond 3955 is like a super strong glue used in cars, machines, and even phones. It sticks fast, handles heat well, and stays flexible. No fancy tools are needed, just apply and it sets quickly, giving a rubbery finish that’s tough against moisture and temperature changes. It’s perfect for keeping things together securely!
Challenges and Considerations in Lightweighting
Despite the myriad benefits of lightweighting, several challenges and considerations must be addressed to realize its full potential in vehicle design and manufacturing. Technical challenges such as material compatibility, adhesion, and thermal expansion pose significant hurdles to widespread adoption, while environmental and regulatory considerations, including recycling and end-of-life disposal, warrant careful attention to ensure the sustainability of lightweight vehicle design.
Technical Challenges in Integrating Lightweight Materials with Adhesives
Technical challenges abound in integrating lightweight materials such as carbon fiber and aluminum with adhesives, as they possess different thermal expansion coefficients and surface properties that can affect bond strength and durability. Carbon fiber composites, for instance, require specialized surface treatments to promote adhesion and ensure robust bond strength, while aluminum alloys may undergo galvanic corrosion when in contact with certain formulations.
Environmental and Regulatory Considerations for Lightweight Vehicle Design
Environmental and regulatory considerations play a crucial role in shaping the trajectory of lightweight vehicle design and manufacturing, as manufacturers strive to minimize their carbon footprint and comply with stringent emissions standards. Sustainable materials such as bio-based resins and recycled carbon fiber offer promising solutions to reduce environmental impact and promote circular economy principles, while regulatory incentives and mandates incentivize the adoption of lightweighting technologies and practices.
Sustainability Benefits of Lightweighting with Adhesives
When we talk about making cars lighter with adhesives, it’s not just about making them go faster or use less gas. It’s also about being kinder to the planet. When cars are lighter, they produce fewer harmful emissions and use less fossil fuel, which is good news for the environment. By using lighter materials and strong glues like adhesives, carmakers can make vehicles that are more eco-friendly and help fight climate change. So, it’s not just about making cars better, it’s also about making them greener for the world we live in.
Conclusion
In conclusion, adhesives are at the forefront of automotive innovation in 2024 and beyond. From lightweighting and fuel efficiency to safety and structural integrity, these versatile adhesives are driving positive changes in vehicle design and performance.
As automotive manufacturers continue to push the boundaries of technology and sustainability, adhesives will remain a critical enabler of progress. By embracing the power of adhesive applications, we can create a future where vehicles are not only more efficient and eco-friendly but also safer and more enjoyable to drive.
Post a comment